Update time.
While the PCB designing and fab went well and I have a bunch on the way here right now, getting the case prototyped has so far been... unsuccessful. The issue is the miniscule amount of space and the details the case requires. I only had ~1mm extra to work with for length and width when designing the case, which meant a wall thickness of 0.5mm. This is fine (albeit just barely) for injection molded parts made of strong plastic, but for the prototype I've been poking local makers on 3DHubs who have SLA printers (UV cured liquid resin), since FDM printers like mine (that shmoo out hot plastic) aren't accurate enough for this. So far every attempt has resulted in a failure printing either the cover or the case due to that itty bitty wall thickness, and getting the board even this small was like playing entropy bingo for a day. Moving stuff a few mil at a time and seeing what that broke and then moving that new broken thing. Rinse, repeat. The board just isn't getting any smaller at this point with it's current assortment of components.
HOWEVER. Last night I committed the sin of dissecting the most revered game on the Switch, as currently as it's the only cart I own. I'm talking of course about the wonderful Aqua Motor Racing Utopia. I know this hurts us all, but remember, it was for science.
Anyways, I soldered up some magnet wire onto the 3.3V and GND pins, routed them out of the back of the cart, stuck the other ends across my multimeter and wrote down the behavior of the card slot under a variety of circumstances:
1) When the system is in sleep/standby mode, the 3.3V supply is OFF.
2) The slot is powered immediately when resuming from sleep mode. I measured a constant 3.06v.
3) When entering sleep mode, the game slot is powered down for around two seconds, then receives power again for around ten seconds for some reason. It then powers down for good until woken from sleep.
4) When turning off the console, the slot is powered down once the screen backlight turns off, with no resumption of power until the console is booted once more.
5) The card slot is NOT powered in RCM mode. The slot does not receive power until Horizon is loaded and you see the lockscreen appear.
So, there's good news and bad news here. The good news is that I can hijack the 3.3v for stuff when the Switch is on without fear of draining the battery when it's in standby mode or off. This means I can ditch the battery for a supercapacitor! The bad news is that there's no power in RCM mode. This means that AutoRCM would be a Really Bad Idea™, because if your dongle died you would have no way to boot the console to charge your dongle so you could boot the console to
charge your dongle. My angle is that if your RCM jig is built into your dongle, you don't need RCM anyways. If I'm missing an important use case however please let me know.
Moving forward, it turns out that supercapacitors are actually pretty easy to charge and implement if you know your supply voltage will always be consistent. A simple resistor and a diode are all that are needed to limit the charging current and protect against reverse voltage discharge when your input voltage goes low. If anyone would like, I can break out the math, but the short of it is a cap that's about 2/3 the size of the CR1616 I'm using in the first board will work just as well. On a full charge it will last for over an hour with the dongle in sleep mode and be good for a couple dozen payload injections. I'm limiting the current the dongle can get from the Switch to 25mA and even at that miniscule amperage the cap should charge in just a few minutes. This should be well below the current a normal Switch cart needs. If you're wondering what effect 25mA will have on your battery life (remember that the card slot only gives power when the system running, current drain is 0 when in standby or off), the Switch has a 4310mAh battery pack @ 3.7v. 25 / 4310 is 0.058, or about half a percent of your battery life for every hour the Switch is running on battery.
So that leaves me where I am now, which is making a new PCB. The schematic is already done. Thanks to the supercap being substantially smaller than the battery, I should be able to add enough meat to make the case printable on an SLA (and possibly even FDM) printer. Day job runs long this week so it will likely be late Friday I'm back here with shiny renders of the new design.
Attached is the current WIP schematic for those interested as well as a picture of me violating my switch with magnet wire.
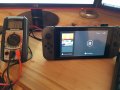